Pre-processing
Peregrine receives hazardous waste from various industrial sectors like pharmaceuticals, chemicals, etc. having different physical and chemical properties. These wastes are treated chemically and physically to bring them to a uniform characteristic and convert into appropriate form for its optimum utilization in co-processing.
Such waste material used for co processing are referred to as Alternative Fuel Resources (AFR).
Received Liquid solvents are carried to site in Tankers or barrels and are transferred into the properly designed storage tanks. Nitrogen blanketing is to be present in the tank to avoid any vapors coming out of the storage tank to atmosphere.
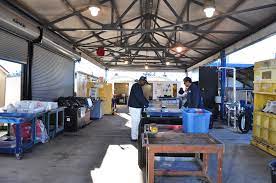
Hazardous Waste Handling
- Liquid solvents are unloaded by using pumps, filtered and are transferred to storage tanks.
- Storage tanks are coated inside with Special lining to avoid corrosion and required safety equipment are provided.
- Agitator is provided in the tank for maintaining the homogeneity of the liquid.
- Grounding system is provided to neutralize the static charges developed during the transfer of liquid.
- Liquid stored in the tank is filtered and thus transferred for firing.
- Seal-less Pumps are used for the transfer of liquid from the storage tank.
- Lined Pipes, bends and fittings are used for conveying of the liquid.
- Control Valves, Transmitters and Switches are provided for easy monitoring and control of the system.
- Drain out Pump is provided for removing the liquid from the line during an emergency.
- Drain out valves are provided in the line.
Hazardous Waste Disposal
Alternate Fuel Resource (AFR) prepared after pre-processing is sent to various industries who use Alternate Fuel Resource (AFR) for co-processing. Co processing ranks higher in the waste processing hierarchy for the following reasons:
- High flame temperature (2000°C) – ensures complete destruction of harmful pollutants.
- Residence time of combustion gases above 1000°C in excess of 3-4 seconds – ensures complete destruction of pollutants.
- Complete destruction of organic compounds.
- Total neutralization of acid gases, sulphur oxides and hydrogen chloride, by the active lime in the kiln load, in large excess to the stoichiometry.
- Embedding of the traces of heavy metals in the clinker structure with very stable links (metallic silicates formation).
- No production of by-products such as ash or liquid residue from gas cleaning.